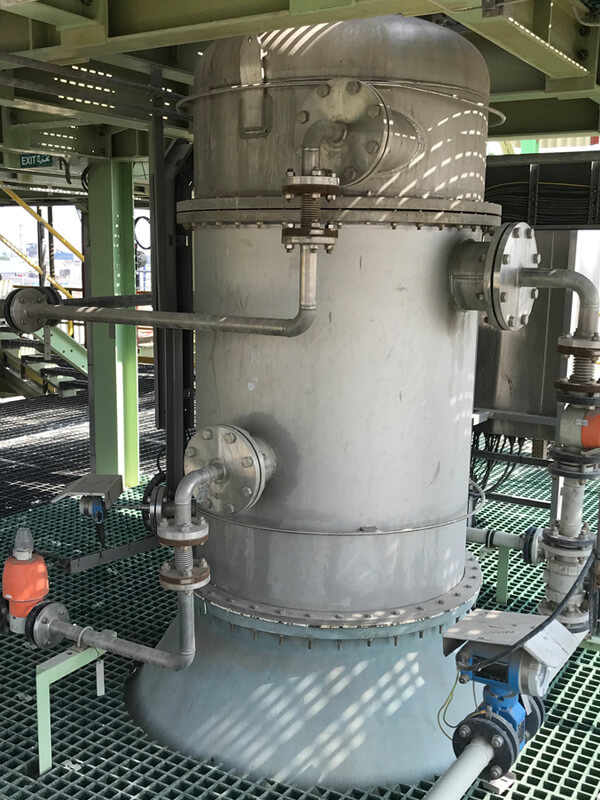
Quench Vessels
Quench vessels are used to rapidly cool hot flue gas, process gas or syngas. ERG has extensive experience of high temperature quenching as the first stage of a wet gas cleaning package, see examples of typical applications here.Operating Principle
A quench vessel is usually configured for vertical gas flow with the inlet nozzle at the top. The hot gas enters the vessel and is immediately sprayed with the quench liquor. The gas is cooled by a process called adiabatic saturation – a portion of the sprayed quench liquor evaporates and the energy to achieve this evaporation is taken from the hot gas, so causing its temperature to drop. The gas cools to what is known as the adiabatic saturation temperature, or quench temperature, which depends on the inlet gas temperature, humidity and dry gas composition. The quenched gas then passes to the next treatment stage of the gas cleaning package, and the remaining quench liquor drains under gravity into a sump tank from where it is recirculated back to the top of the quench vessel. The inlet gas temperature is dependent on the process. ERG has experience of providing quench vessels for:- Oxidiser flue gases in the range 850 to 1,150 oC, containing sulphurous and/or halogenated contaminants and particulates
- Process gases up to 500 oC, also containing sulphurous and/or halogenated contaminants and particulates
- Syngases up to 250 oC, containing VOCs, ammonia, halogenated and sulphurous contaminants and tars
Design Features
- Materials of construction. ERG matches the quench vessel materials to the process requirements: the contaminants and the operating temperature. Typically, quenches are fabricated in 316 SS, duplex, hastelloy C276 or brick lined carbon steel.
- Process safety – emergency water. ERG’s designs include for an emergency water supply which comes on automatically if there is a problem with the main quench liquid circuit. This is used to protect the downstream equipment from potential heat damage.
- Design for robust operation. ERG’s quenches are designed to limit corrosion in the wet dry zone at the top of the vessel and erosion where particulates are present, and they feature easy access for inspection and maintenance of internal parts.
- Process control. Careful control of the liquid operating temperature is needed to prevent problems downstream, for example with sub micron aerosol mist. ERG’s design, system controls and O&M requirements combine to ensure the smooth operation of the plant.
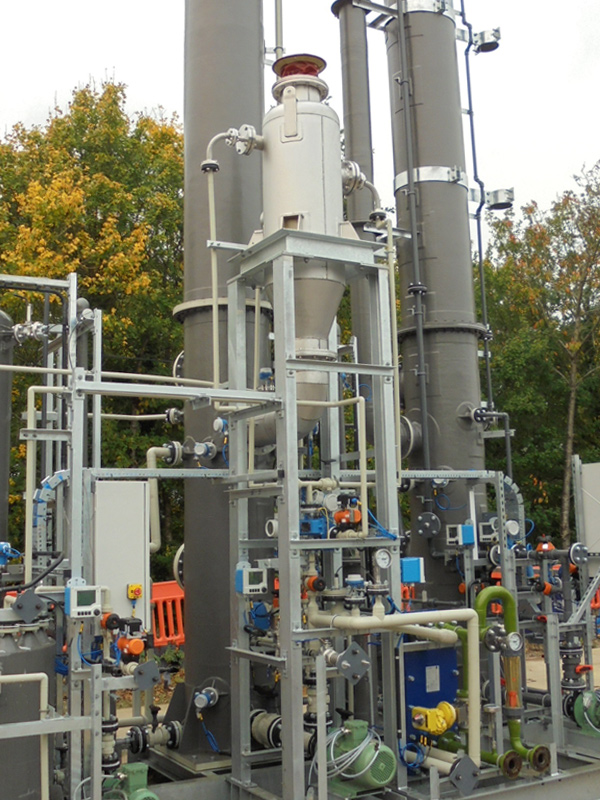
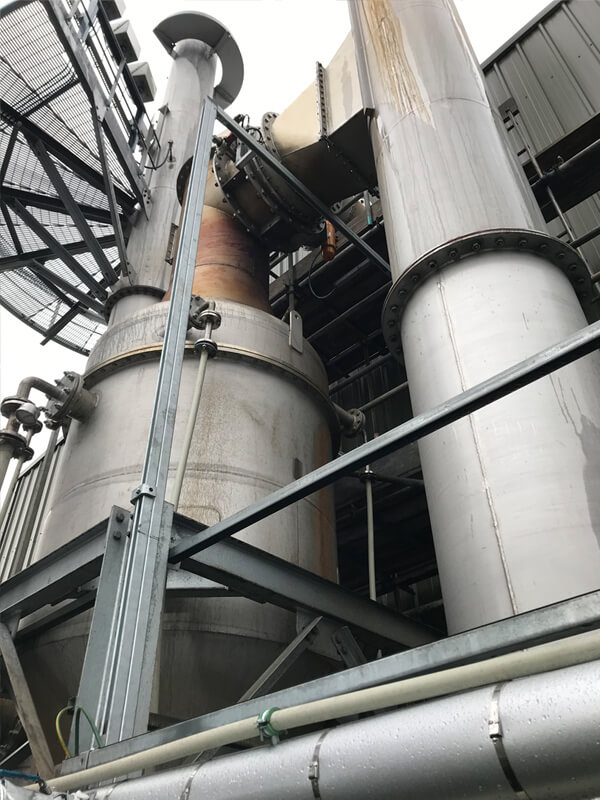
As well as quench vessels as described, ERG can also provide partial quenches using air or water to reduce the gas temperature without achieving complete adiabatic saturation.
ERG quench vessels are provided as part of complete scrubbing packages, with the necessary sump tank, expansion bellows, fan, ductwork, pump, pipework and controls. In the majority of applications, the quench is combined with other ERG heat transfer equipment (venturi, tray tower, packed tower, V tex® scrubber, etc).
Refer to our other mass transfer technologies for full details of the range.
Quench Vessels
Quench vessels are used to rapidly cool hot flue gas, process gas or syngas. ERG has extensive experience of high temperature quenching as the first stage of a wet gas cleaning package, see examples of typical applications here.Operating Principle
A quench vessel is usually configured for vertical gas flow with the inlet nozzle at the top. The hot gas enters the vessel and is immediately sprayed with the quench liquor. The gas is cooled by a process called adiabatic saturation – a portion of the sprayed quench liquor evaporates and the energy to achieve this evaporation is taken from the hot gas, so causing its temperature to drop. The gas cools to what is known as the adiabatic saturation temperature, or quench temperature, which depends on the inlet gas temperature, humidity and dry gas composition. The quenched gas then passes to the next treatment stage of the gas cleaning package, and the remaining quench liquor drains under gravity into a sump tank from where it is recirculated back to the top of the quench vessel. The inlet gas temperature is dependent on the process. ERG has experience of providing quench vessels for:- Oxidiser flue gases in the range 850 to 1,150 oC, containing sulphurous and/or halogenated contaminants and particulates
- Process gases up to 500 oC, also containing sulphurous and/or halogenated contaminants and particulates
- Syngases up to 250 oC, containing VOCs, ammonia, halogenated and sulphurous contaminants and tars
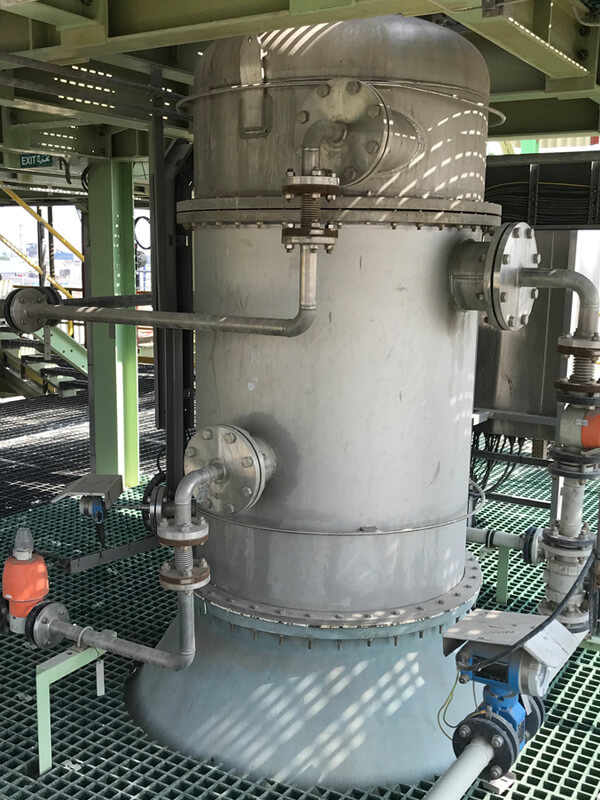
Design Features
- Materials of construction. ERG matches the quench vessel materials to the process requirements: the contaminants and the operating temperature. Typically, quenches are fabricated in 316 SS, duplex, hastelloy C276 or brick lined carbon steel.
- Process safety – emergency water. ERG’s designs include for an emergency water supply which comes on automatically if there is a problem with the main quench liquid circuit. This is used to protect the downstream equipment from potential heat damage.
- Design for robust operation. ERG’s quenches are designed to limit corrosion in the wet dry zone at the top of the vessel and erosion where particulates are present, and they feature easy access for inspection and maintenance of internal parts.
- Process control. Careful control of the liquid operating temperature is needed to prevent problems downstream, for example with sub micron aerosol mist. ERG’s design, system controls and O&M requirements combine to ensure the smooth operation of the plant.
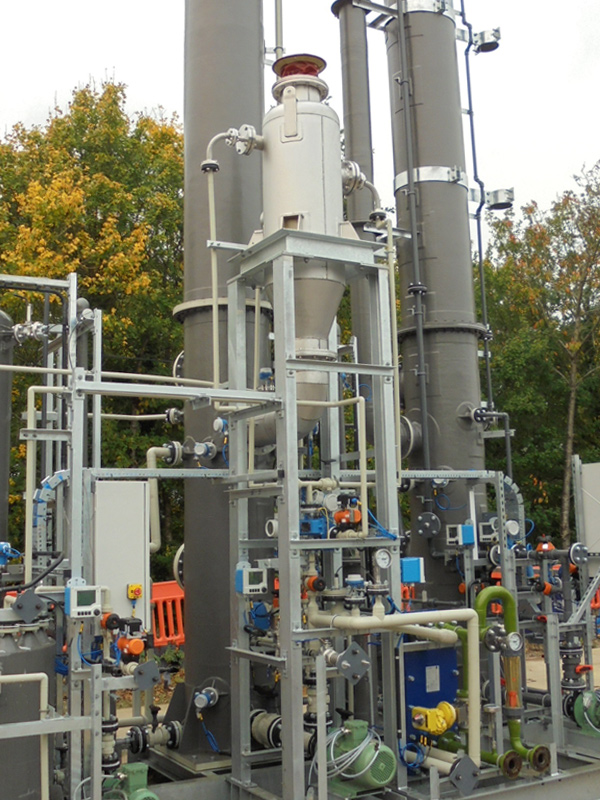
As well as quench vessels as described, ERG can also provide partial quenches using air or water to reduce the gas temperature without achieving complete adiabatic saturation.
ERG quench vessels are provided as part of complete scrubbing packages, with the necessary sump tank, expansion bellows, fan, ductwork, pump, pipework and controls. In the majority of applications, the quench is combined with other ERG heat transfer equipment (venturi, tray tower, packed tower, V tex® scrubber, etc).
Refer to our other mass transfer technologies for full details of the range.
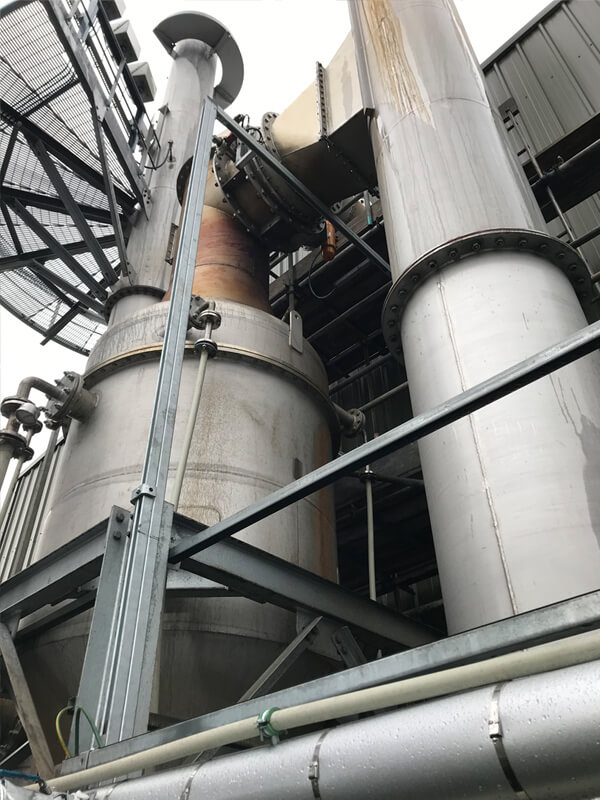